The Covid-19 pandemic has disrupted the global car supply chain.
- RSM Việt Nam
- Sep 29, 2023
- 5 min read
Updated: Oct 5, 2023
2020 is considered a transformational year for the global car manufacturing industry. However, Covid-19 has become one of the biggest challenges for the supply chain.
2020 is considered a transformational year for the global automotive manufacturing industry. However, Covid-19 has become one of the biggest challenges for the supply chain.
The car industry has borne the impacts of the disease outbreak extending beyond China's borders, as the shortage of supplies from China led to a halt in production worldwide. While China is not an exporter of fully assembled cars, it has become a crucial part of the global car component and parts network. In 2018, China achieved nearly $35 billion in exports of car parts, with the United States importing nearly $12 billion.
In the Chinese car market, major brands such as Volkswagen and GM sell millions of vehicles each year, accounting for 40% of the global total sales. Faced with the challenging situation during the pandemic, many experts are concerned about the potential severe business losses for these companies. Additionally, a majority of the components and parts of a car are also manufactured in the world's most populous country.

Nissan has announced the temporary suspension of car production in Japan due to the ongoing pandemic outbreak. Hyundai, a company heavily reliant on Chinese suppliers, temporarily halted operations at three of its plants in South Korea in February due to parts shortages. By mid-March, most major car manufacturers in the UK and Europe had either temporarily suspended or reduced production due to disruptions as the pandemic continued to spread. However, some lower-volume manufacturers like Aston Martin have kept their plants operational.
In the coming period, the recovery prospects for Vietnam's car industry remain uncertain and depend on the pandemic situation. If the situation continues to be complex and the supply chain is significantly affected, some car assemblers may have to temporarily halt production, and certain plans may be postponed in the near future.
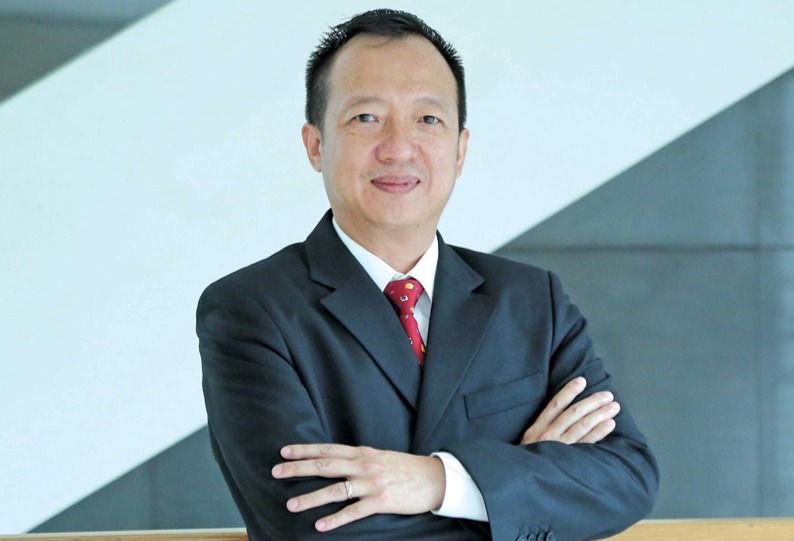
Mr. Le Khanh Lam, Deputy director of tax and advisory services at RSM Vietnam
As car manufacturers attempt to reopen their plants and production facilities, many suppliers have no choice but to resort to costly air freight transportation for components instead of using sea freight in order to quickly deliver the parts to their customers. Supply chain issues may force companies to repatriate workers or reduce production in the near future. When the Covid-19 pandemic hit Italy, the world's 8th largest economy, Lamborghini announced the closure of its Sant’Agata Bolognese plant. This facility was responsible for producing all Lamborghini models, meaning no new Lamborghinis were being manufactured. Additionally, Fiat Chrysler also temporarily closed four plants in Italy.
In the midst of the Covid-19 pandemic, car companies worldwide are increasing remote work arrangements among their employees within manufacturing plants. This will impact changes in production processes and reduce daily production capacity. These changes, coupled with allowing employees to work from home, pose significant challenges for companies in meeting global car production demands.
The car supply chain in Europe is highly integrated, with supply chains spanning multiple countries. Germany serves as the global headquarters for Volkswagen, BMW, and Daimler. On the other hand, Renault and Peugeot, merged with Fiat Chrysler, have their headquarters in France. As the Covid-19 situation in both France and Germany shows no signs of abating, and with continuous measures being implemented to curb the spread, car manufacturers in these countries are experiencing significant disruptions in their supply chain networks as well as their business operations.
How Covid-19 is transforming the auto manufacturing industry
Significant growth in the automotive manufacturing market may occur as manufacturers continue to resume operations, but it will take more time to reach previous production levels. The outbreak of the pandemic is undoubtedly accelerating the process of consolidation and transformation in this industry, with businesses focusing on recovery capabilities, innovation, and increased investment in emerging growth markets. The significant disruptions caused by the pandemic have prompted companies to respond by diversifying their suppliers, resulting in higher short-term costs.
These higher costs will gradually decrease as supply chain disruptions diminish. However, manufacturers are shifting their global supply chains away from China in response to tackle policies while reducing dependence on this source of supply. This event marks the exit from China after more than three decades of manufacturing relocation to the country. In this context, Vietnam has an advantage in attracting investors due to factors such as its ability to effectively control the pandemic and the ability to quickly recover the economy.
However, the process of shifting production to Vietnam also faces several challenges. In the short term, manufacturers may encounter difficulties in relocating production due to the need to reorganize their supply chains. Moreover, companies often find themselves in a dilemma when deciding on the new location and market entry strategy. These issues will significantly impact the competitive capabilities of businesses. Therefore, companies need to make informed decisions to ensure stable production operations in the short term while expanding their business when necessary.
Handling changes
Here's what experts from RSM suggest in preparing for short-term changes:
Bringing stability to the supply chain, maximizing liquidity, and putting customers at the center are urgent issues in the short term to improve the financial situation in the car manufacturing industry.
Firstly, stabilize the supply chain. The pandemic has brought about a series of risks and impacts on the entire supply chain. Consequently, the process of moving components from supply to production and ultimately distribution requires many complex decisions. Establishing alternative supply chain options through intelligent problem-solving helps determine the best choices to bring short-term stability and lay the foundation for long-term success. In the domestic market, businesses have been tirelessly working to stabilize the supply chain while preparing for economic recovery at any time.
Secondly, maximize liquidity. The nature of the car industry requires significant capital, heavy investment in development, and research to enhance value. Instead of focusing solely on profitability metrics, companies should shift their focus towards improving liquidity. Managing cash conversion cycles and optimizing the use of internal working capital, including payables, receivables, and inventory, should be a priority. Additionally, there should be coordination within the organization to implement and define performance metrics to maximize the liquidity of assets. On the other hand, businesses need to assess their existing credit limits based on market conditions and consider alternative sources of liquidity to meet working capital needs when necessary.
Thirdly, prioritize the customer. Businesses should focus on meeting the evolving needs of customers during these turbulent times. Making the customer the focal point is a core value that businesses should emphasize, directing their goals toward customer demands. This criterion in the future will have significant impacts on supply chain design to meet increasingly complex customer requirements.
Providing stability to the supply chain, maximizing liquidity, and focusing on customers are urgent priorities in the short term to improve the financial situation of car manufacturing businesses. However, for the industry to recover after the pandemic, it requires a strong commitment from businesses to adapt to the changes during this volatile period, along with an emphasis on investing in emerging growth markets to sustain and rapidly develop. This will be the guiding principle for businesses in the industry.
Author: Mr. Le Khanh Lam - Deputy General Director of RSM Vietnam
Comments